Wood Pellet Making Machine
Biomass wood pellets have wide range application in boiler, power plants, factories and household heating, wood processing plant etc.
Features for Wood pellet making machine
- 1.Raw material: woodiness, straw, peanut shell, palm nut, coconut shell, cotton seed, elephant grass, sugar cane, olive slag etc.
- 2.Suitable for family and workshop production, small footprint.
- 3.Siemens motor, imported bearing.
- 4.Driven by bevel gear, high efficiency of transmission, stable and smooth transmission.
- 5.With automatic lubrication system, stop refueling is not required, which will save costs and protect the roller better.
- 6.Forced feeder: With observation window, it can also used for refueling mouth each time the machine is turned on/off.
- 7.The protection device for main shaft is equipped to prevent the main shaft broken.
- 8.Thicken and strengthen design for the machine body, hollow shaft, main shaft and driving wheel, guarantee machine rigidity.
- 9.Connect the motor and transmission box with serpentine steel flex coupling, convenient for disassembly and maintenance.
- 10.Split installation for transmission wheel and hollow shaft, convenient for disassembly and maintenance.
Technical Parameters for Wood pellet making machine
Model | Capacity (t/h) | Power (kw) | Inner diameter of die (mm) | Pellet size (mm) | Dimension (mm) | Net weight (T) |
YPM250 | 0.1-0.2 | 15 | 250 | Ø6,Ø8,Ø10 | 1420*1200*1400 | 1 |
YPM320 | 0.3-0.5 | 37 | 320 | Ø6,Ø8,Ø10 | 2200*1000*1900 | 2.5 |
YPM350 | 0.5-0.8 | 55 | 350 | Ø6,Ø8,Ø10 | 2500*1100*2000 | 3.5 |
YPM420 | 1-1.5 | 110 | 420 | Ø6,Ø8,Ø10 | 2800*1150*2100 | 4 |
YPM520 | 1.5-2.5 | 160 | 520 | Ø6,Ø8,Ø10 | 3200*1500*2500 | 5 |
YPM660 | 2.5-3.5 | 185 | 660 | Ø6,Ø8,Ø10 | 3600*1700*3300 | 6 |
YPM800 | 3.5-5 | 250 | 800 | Ø6,Ø8,Ø10 | 3900*1800*3200 | 8 |
How to use Wood pellet making machine to make biomass pellets
Biomass pellets have wide range application in boiler, power plants, factories and household heating, wood processing plant etc.
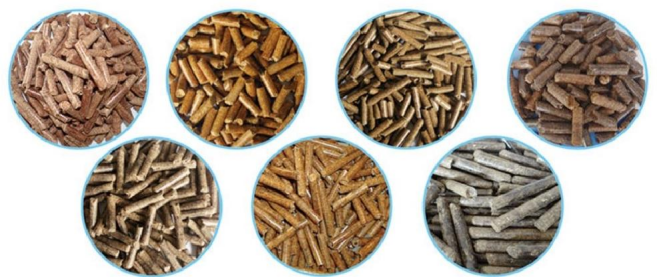
1.Debarking: If the raw material is wood log with tree bark, we use a wood debarker to take out offer the bark. If the raw materials is other like straw, rice husk, sawdust, woodchips etc, it is no need to use the debarker.
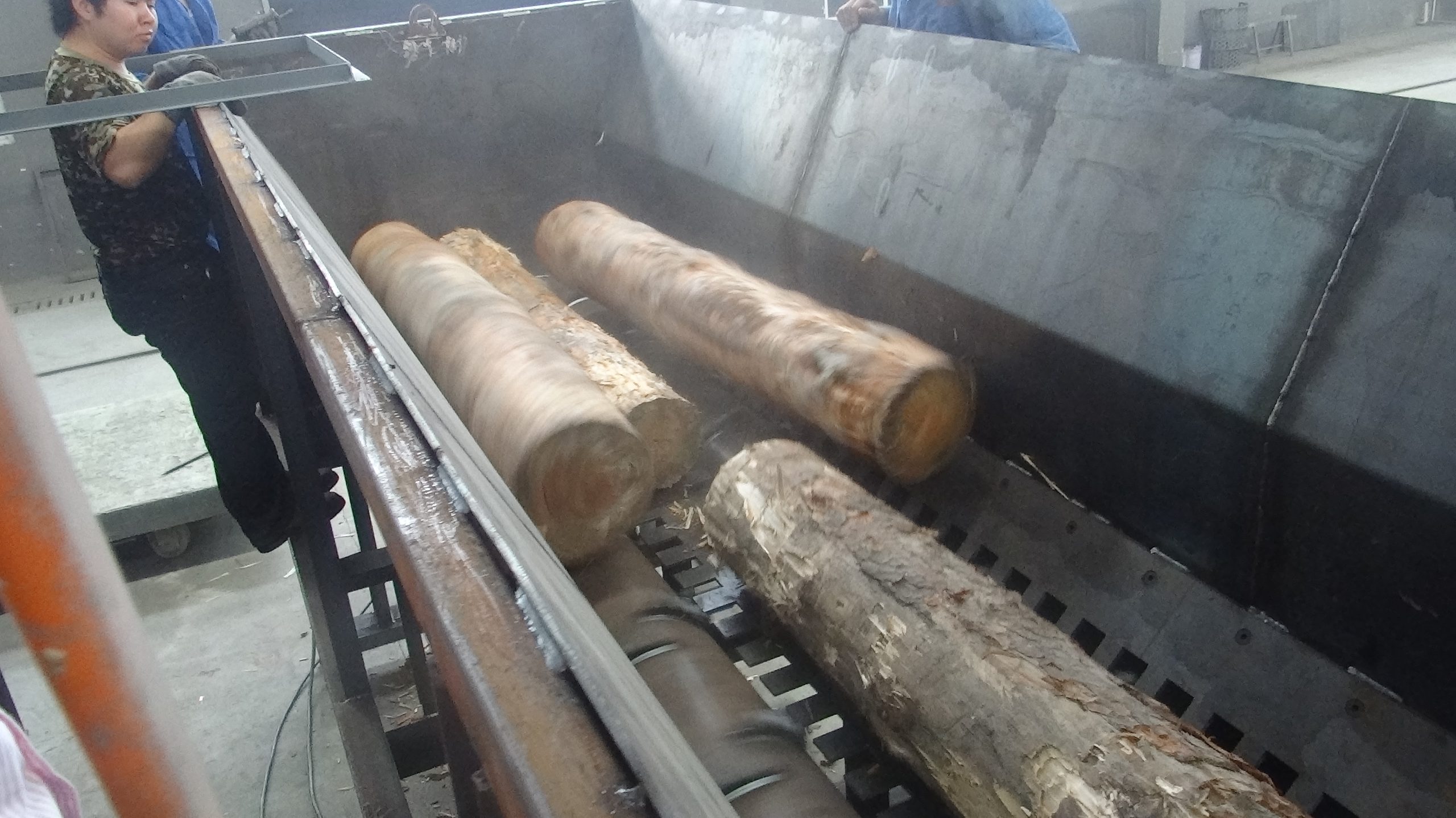
2.Chipping: Use a chiper to cut the straw, branch materials, and large pieces that cannot be directly crushed into small pieces.
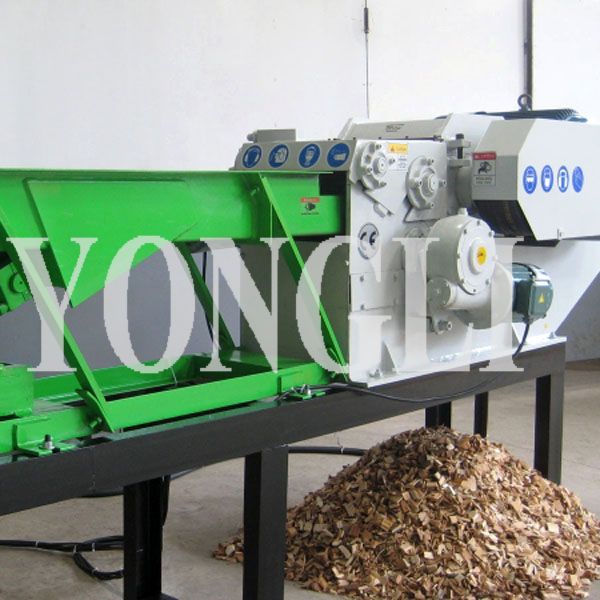
3. Crushing: The raw materials is crushed by a hammer mill to make the particle size less than 5mm. The hammer mill is only equipped with a feed port and a discharge port. The feed port is closed after feeding to reduce dust escape. The discharge port is connected to a cyclone separator. The cyclone separator uses the principle of centrifugal force to separate the scraps, and the scraps are deposited in the dust collector , The gas is discharged through the material port, and the gas is discharged from the cyclone separator and then processed by the pulse filter. All the collected dust is recycled to the pellet production line.
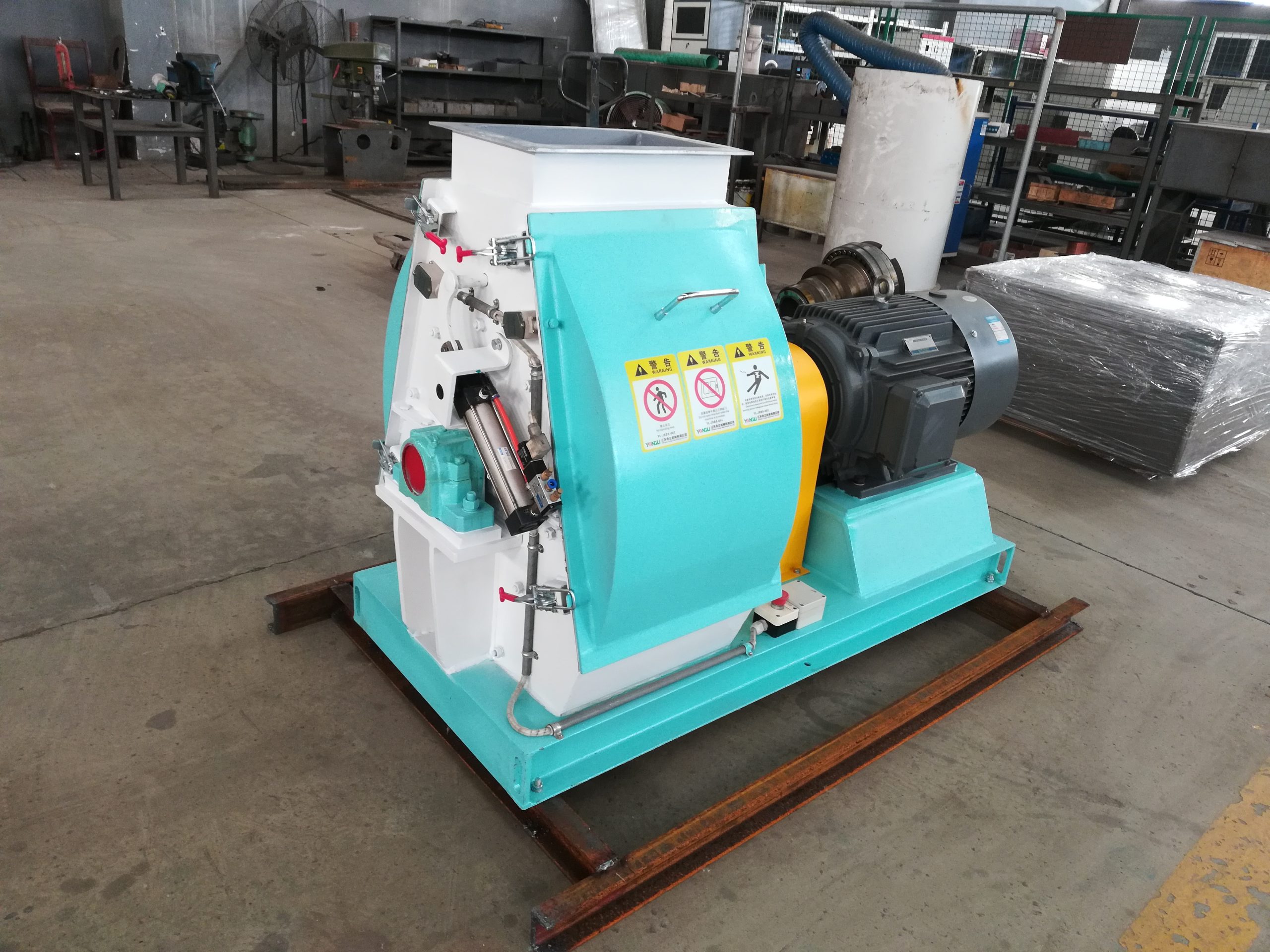
4.Drying: Some raw materials have a moisture content of 55% or over more higher up to 65%, which does not meet the requirements of pellet press. These raw materials with excessive moisture content need to be dried to make the moisture content meet the granulation requirements,and the moisture content of the raw materials after drying is about 10%. The dryer of this project is equipped with a biomass burner, and the fuel is biomass pellets produced by the pellet line project.
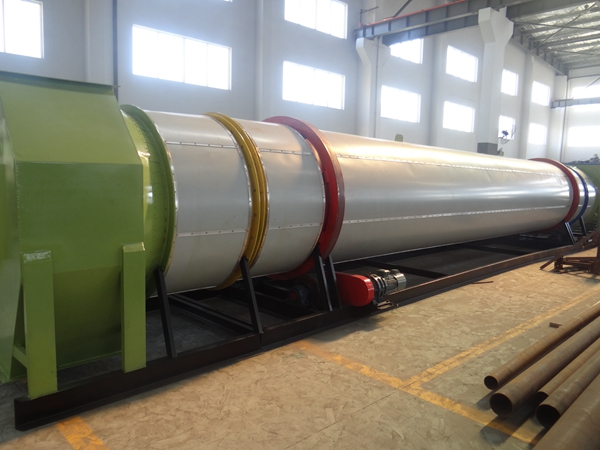
5.Conveying and feeding: the raw materials are sucked into the feed port of the pellet machine through the feeding auger.
6.Pelleting: the raw materials are fed into the pellet machine through the feeding auger, and the finished pellets is formed by extrusion molding. The extrusion process is a physical process without any adhesive and no chemical reaction occurs, except for the feeding auger connection The equipment is sealed at and outside the discharge port.
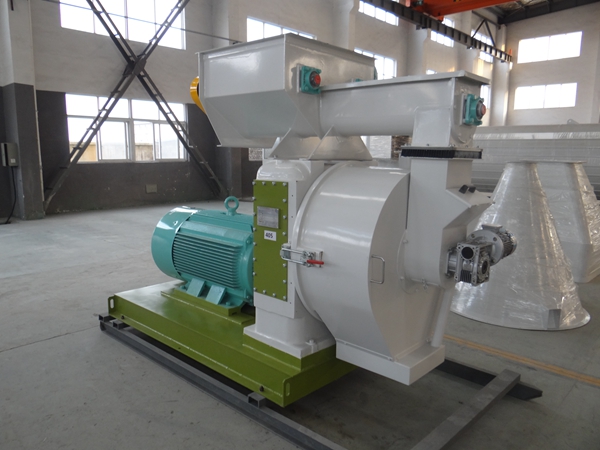
7.Lifting,conveying and cooling: The pelletized biomass pellets are naturally cooled by conveying, so that their temperature can reach the conditions of packaging and storage, and finally conveyed to the finished product warehouse. This process generates dust and noise.
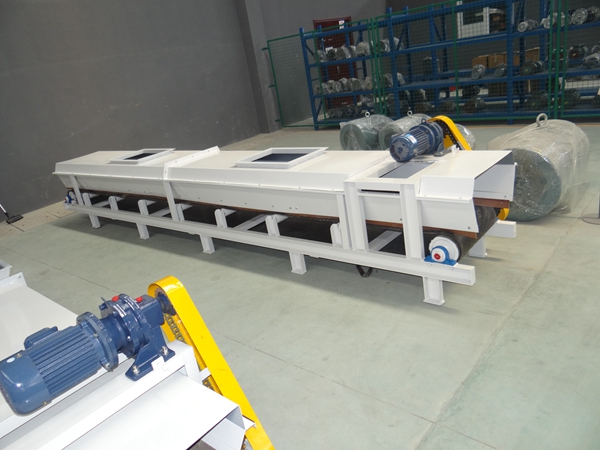
8.Pellet packing and palletizing:The compressed hot pellets pass through the screening at the end of the belt conveyors, and the qualified biomass pellets fall into the finished product warehouse. The bottom of the finished product warehouse is a funnel-shaped discharge port. The finished product can be directly dropped into the packaging bag. After the pellets is packaged by packing machine and palletizing, it could be for sale.
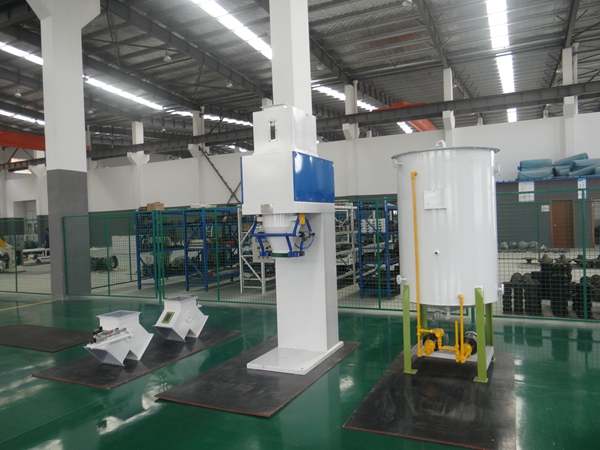